Die 5 häufigsten Fehler bei der MES Einführung
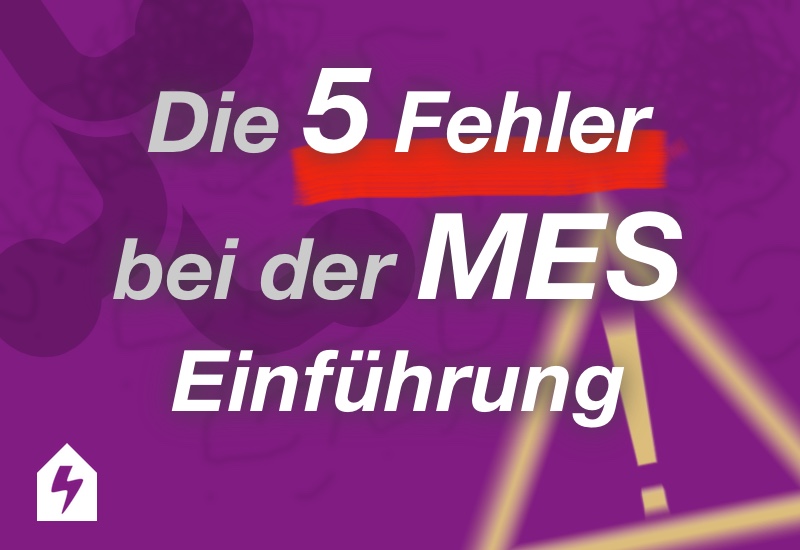
Die Industrie 4.0 lebt von der Datentransparenz im Unternehmen. Doch häufig ist das der Fall. Im Produktionsumfeld erweisen sich historisch gewachsene IT-Strukturen als unflexibel, undurchschaubar und nur schwer anpassbar. Das Ergebnis ist: Fertigungsprozesse und die Analyse von Fertigungsdaten sind ineffizient und sorgen für Frust bei der Auswertung. Die Lösung sind so genannte „Manufacturing Execution Systeme“ (MES). Sie bilden das Rückgrat für alle Arten von Daten im Produktionsumfeld und sorgen damit für Flexibilität und Transparenz auf dem Shopfloor. Doch der Weg ist häufig steiniger als man vor einer MES Einführung glauben möchte.
Jedes Unternehmen ist auf seine Art und Weise einzigartig und es gibt kein Patentrezept, um binnen kurzer Zeit schnell zum Erfolg zu gelangen. Doch wenn Sie die folgenden 5 Fehler vermeiden, sind Sie einen großen Schritt näher an einer erfolgreichen MES Einführung.
1. Unzureichende Netzwerk-Infrastruktur
Die grundlegende Voraussetzung für eine erfolgreiche MES Einführung ist ein flächenleckes Netzwerk in der Produktion. WLAN ist keine Option, da die Signalstärke und Erreichbarkeit zwischen Maschinen und Metallschränken nicht sichergestellt werden kann. Die Folge ist, dass Daten unwiederbringlich verlorengehen oder Eingaben durch Mitarbeiter zu lange dauern und die Handhabung unzumutbar wird.
2. Vielzahl an Schnittstellen
In den meisten Fällen wird ein MES zusätzlich zum bestehenden ERP-System installiert. Die Folge ist, dass Informationen wie Fertigungsaufträge, Stücklisten, Arbeitsplätze, Personalstamm, etc. in beiden Systemen vorhanden sein müssen. Dadurch ergeben sich eine Fülle an Schnittstellen, die häufig kundenspezifisch angepasst werden müssen, denn kein ERP-System ist wie das andere. Sogar wenn das MES und ERP System vom selben Hersteller kommen, können durch Anpassungen die Systeme unterschiedlich funktionieren. Was bei dem einen Unternehmen an Stammdaten erforderlich ist, kann bei einem anderen zuviel sein.
Jedes Modul (Fertigungsaufträge, Rückmeldungen, Instandhaltung, Personalstamm, Zeiterfassung, usw.) benötigt individuelle Schnittstellen und für deren Implementierung und Anpassung muss ausreichend Zeit eingeplant werden.
3. Mangelndes Prozessverständnis
Projektleiter benötigen für die Implementierung eines MES ein übergreifendes Prozessverständnis, denn hier greifen mehrere Abteilungen, Arbeitsabläufe und Softwaremodule ineinander. Davon betroffen ist die Auftragssteuerung, die Urlaubsplanung der Personalabteilung, sowie die Instandhaltung und die Personaleinsatzplanung. Kurzum, es ist erforderlich, ein Allrounder zu sein, um nicht jedem Problem hinterher zu laufen und noch schlimmer, vorhersehbare Probleme nicht rechtzeitig zu sehen. Auch die Akzeptanz der Mitarbeiter kann positiv beeinflusst werden, wenn der Projektleiter ein umfassendes Prozessverständnis hat und das Einführungsprojekt die jeweiligen Anforderungen sachgerecht berücksichtigt.
4. Schlechte Abstimmung mit dem Betriebsrat
Ein MES ist die Brücke zwischen der Produktions- und Planungsebene. Mit so einem System schafft ein Unternehmen Transparenz in der Produktion und allen umliegenden Prozessen. Das sorgt mittelfristig zur Steigerung der Qualität und sorgt für eine Reduzierung der Fertigungskosten. Durch diese Transparenz besteht die Gefahr, dass das MES auch für die Leistungs- und Verhaltenskontrolle genutzt werden kann. Aus diesem Grund hat der Betriebsrat bei der Einführung solcher Systeme ein Mitbestimmungsrecht. Nicht ohne Grund wird die Einführung solcher Systeme durch den Betriebsrat skeptisch gesehen, da eine Überwachung von Mitarbeitern befürchtet werden kann.
Der Betriebsrat sollte frühzeitig in das Einführungsprojekt einbezogen werden. So kann man den geplanten Einsatzzweck und die technischen Möglichkeiten erläutern. Basierend auf einem gemeinsamen Verständnis der MES Einführung, können Bedenken sachlich ausgeräumt werden sowie technische und organisatorische Maßnahmen getroffen werden, um einen Missbrauch des Systems zu verhindern. Eine Betriebsvereinbarung sorgt für die notwenige Klarheit zwischen den Parteien. Diese sollte klar verständlich formuliert sein und auf unnötigen technischen Jargon verzichten, um das Vertrauen der Mitarbeiter in das MES zu stärken.
5. Unrealistische Erwartungshaltung
„Alle Prozesse und Maschinenzustände sind transparent in einem Dashboard abgebildet.“ - Das ist das Ergebnis langer und intensive Arbeit an der Digitalisierung im Unternehmen. Wenn ein MES auf die bestehenden Prozesse und Abläufe aufgesetzt wird, dann bedarf es einer Menge Zeit und Engagement, um das Ziel nicht aus den Augen zu verlieren. Die Erwartungshaltung der Chefs ist auf der anderen Seite nicht schnell genug zufrieden zu stellen. Das erhöht den Druck auf den Projektleiter und vor allem auf das Projektteam. Somit wandert der Fokus weg von der grundlegenden und nachhaltigen Harmonisierung der Systeme hin zu schnell vorzeigbaren Ergebnissen. Doch „quick-&-dirty“-Lösungen halten meistens nicht lange und verursachen mittelfristig mehr Arbeit.
Nach einer langen Implementierungszeit und den ersten Erfolgen folgt die Tatsache, dass mit schönen Dashboards und Auswertungen noch nichts verändert und keine Verbesserung herbeigeführt wurde. Das neue System muss über Jahre genutzt und gelebt werden. Am Ende sind es die Menschen selbst, die mit der Datentransparenz Veränderungen durchsetzen können.
Fazit
Lassen Sie sich nicht aus der Ruhe bringen und verfolgen Sie Ihre Ziele. Nehmen Sie den Anbieter in die Pflicht, die Prozesse bei Ihnen intern zu verstehen und fordern Sie bei der Implementierung Zahlungen nach einem Fortschrittsplan. Beim Hausbau werden Zahlungen auch nach Baufortschritt freigegeben.
Prüfen Sie vorab, ob Sie ein großes und umfangreichen MES benötigen oder Sie bereits mit kleinen Lösungen wie Maschinendaten- und Störungszeiterfassung große Hebel bewegt bekommen. Auf dieser Basis lassen sich bereits elegante Dashboard generieren und liefern wertvolle Informationen, um die Produktion zu optimieren. Details findet man am Ort des Geschehens häufig besser begründet als in Kennzahlen im Dashboard.
Das primäre Ziel der Implementierung eines MES ist es, vorhandene Reserven aufzudecken, diese zu nutzen und letztendlich die Produktionskosten zu senken und die Wettbewerbsfähigkeit des Unternehmens zu steigern. Damit verbunden die Arbeitsplätze der Mitarbeiter am Standort zu erhalten.
© 2019 - 2025 Powerhouse Solutions GmbH